Before any of your favorite goods and supplies ever make it into the markets and the stunning displays of online shops, it goes through a long and tedious production process of manufacturing. A successful product plan traces its roots to an efficient manufacturing budget. This financial document accounts for all the necessary material and labor costs that go into producing the best output. Learn more about this below.
FREE 10+ Manufacturing Budget Samples
1. Manufacturing Budget Template
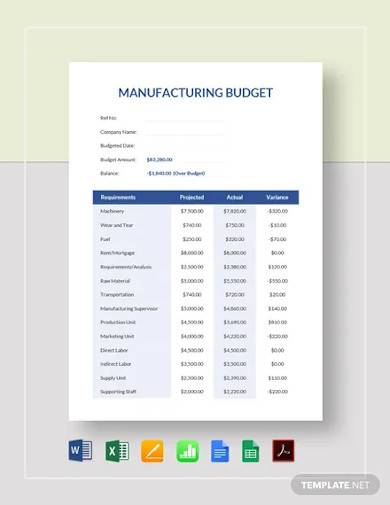
2. Manufacturing Production Budget Template
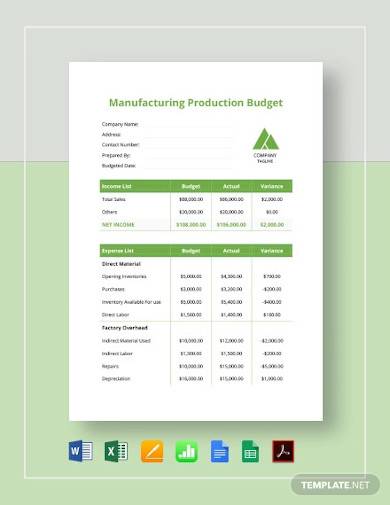
3. Manufacturing Company Budget Template
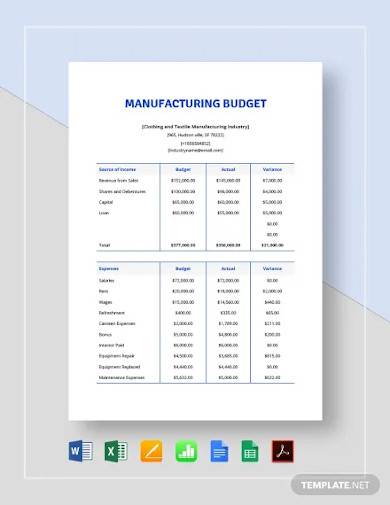
4. Manufacturing Overhead Budget Template
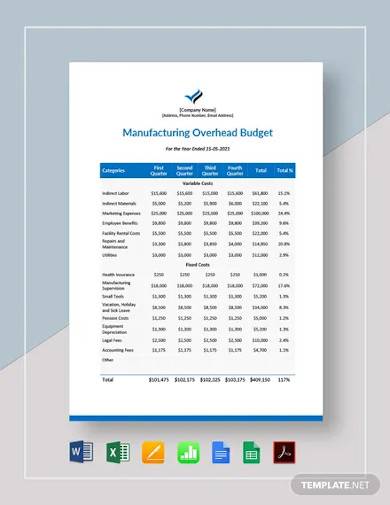
5. Free Manufacturing Budget Template
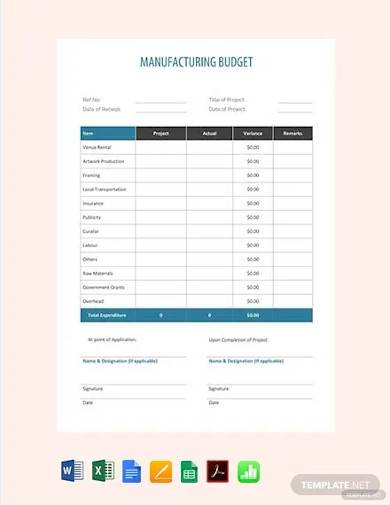
6. Sample Manufacturing Budget Template
7. Sample Manufacturing Budget
8. Manufacturing Project Budget Template
9. Production Budget Template
10. Manufacturing Budget Form Sample
11. Sample Manufacturing Overhead Budget
What Is a Manufacturing Budget?
A manufacturing budget contains the costs and items needed to produce a product. This is a useful document in tracking the production expense and determining the selling price of a product when introduced to the market. This includes direct materials, labor costs, and the overhead budget according to the number of product units.
Dos and Don’t of Manufacture Budgeting
As of 2018, the manufacturing industry in the US amounted to $2.33 trillion. This accounts for approximately 11% of the country’s economy. It contributed 12.69 million employments. While the industry used to occupy over 24% of the country’s economy n the 1970s, it’s undeniable that it’s still among the country’s business giants and an essential part of its ever-booming economic activity.
According to IBISWorld, the country houses 565,537 manufacturing businesses as of 2020. With competition as vast as that number, it can be challenging to keep up and keep the operation up and running. A way to make it work for you is to have a solid manufacturing budget to fund your process. Here are some dos and don’t of manufacture budgeting that you should remember:
Dos
1. Do design your budget in a way that meets your financial goals.
2. Do consider putting enough overtime instead of extending the work schedule.
3. Do limit your financial projections before aiming for longer periods.
4. Do avoid relying too much on previous budget plans. Things can change with your current setting. Explore the present more.
Don’ts
1. Don’t take the labor and material costs during the pre-production stage lightly.
2. Don’t forget to consider emergency expenses and other forms of disruptions that can halt your operations.
3. Don’t get frustrated when you need to make several adjustments throughout the process. Make your budget flexible to changes.
How to Make a Manufacturing Budget
Here are useful steps to help you make a manufacturing budget:
1. Start With an Expenses List
Begin your manufacturing budget by identifying the list of your expenses. Although this varies according to the type of industry you’re in and how your production process goes, this typically involves the overhead budget and the production budget. The production budget consists of all items directly involved in the production of the product or the direct costs. All the raw materials and the labor goes under its panel. On the other hand, the overhead budget is indirect costs pertaining to variable items on your budget sheet. Determine all the activities associated with the manufacturing and identify what activities you need to fund to help have a complete account of all expenditures of the manufacturing process.
2. Integrate the Right Price
Include accurate price details on your budget to develop a budgeting plan that can help you perform decisions and assess your finances. If you’ve been in the business for quite some time, you can put in the right amount for the direct costs for the production and decide on your variables as you go along. This results in a projected cost where you can decide to cut down your expenditures or increase your allocation on certain items on your budget. However, if you’re new to the business and are trying to come up with a proposal or a budget estimate, you can do research and find out how much the production process will cost you.
3. Consult Past Records
The past is never left in the past when it comes to business. Every previous record can be a significant resource in the future. This is why archiving business documents is a must for every enterprise. Consulting past financial plans and records of your manufacturing business can help you shape your manufacturing budget. This helps you determine what items to put on your list, what variables you can use on your operations, how you’re going to stretch a tight budget, and other relevant information that can serve as an integral idea to your planning. You’ll also be able to identify what burdened you in the past, so you can make present corrections and act with more caution in the present.
4. Keep Your Budget Flexible
Your budget should cover a specific period or timeline. It can be a monthly budget, an annual budget, or a quarterly budget. Along the way, you will have to make necessary changes when something is not working out or your need for significant emergency repairs or purchases. Unexpected expenses are part of your budget planning. Be sure to make your manufacturing flexible to adjustments and alterations. A rigid budget plan will most likely set you up for failure because not everything is going to turn out as you expect them to be. The best action plan to cope with these changes is to be ready.
FAQs
Is manufacturing costs the same as production costs?
The manufacturing costs only involve the expenses needed to make the production costs pertain to all expenses that come with operating the business.
How do you calculate the total product cost?
Follow these steps in calculating the total products cost:
- Add the total direct material, the labor costs, and the overhead costs
- Divide the sum of the three to the total number of units manufactured through the mentioned components
What are some examples of manufacturing costs?
The examples of manufacturing costs include salaries, machine repair, manufacturing equipment, insurance and taxes, and fixed costs depreciation.
The process of producing high-quality goods is essential to businesses that manage them because their partners will be relying on them. From the distributors to the stores that will display them for all the crowd to see, they’re placing their confidence in your manufacturing’s process quality in supplying them with only the best goods. Our manufacturing budget templates will help plan your manufacturing finances efficiently. Go through our collection and download now!
Related Posts
FREE 13+ Sample Log Sheet Templates in Google Docs Google ...
FREE 9+ Sample Blanket Purchase Agreement Templates in MS ...
FREE 10+ Cost Breakdown Analysis Templates in Google Docs ...
FREE 12+ Sample Business Continuity Plan Templates in PDF
FREE 11+ Sample Performance Evaluation Forms in MS Word PDF
FREE 9+ Warranty Statement Samples & Templates in PDF
FREE 9+ Sample Quality Manual Templates in PDF MS Word
FREE 9+ Contingency Plan Samples in MS Word PDF
FREE 10+ Sample Process Engineer Job Description Templates in ...
FREE 14+ Safety Manual Samples in PDF MS Word
FREE 8+ Industrial Engineer Job Description Samples in MS Word ...
FREE 9+ Bill of Material Samples in MS Word PDF
FREE 10+ Sample Master Settlement Agreement Templates in PDF
FREE 25+ Company Profile Samples in PDF
FREE 6+ Sample Business Model in PDF MS Word