The word ‘quality assurance’ refers to a series of planned, systematic procedures that are taken to ensure that products and services meet certain criteria. It entails not just monitoring the final quality of products to avoid faults, as in quality control, but also systematically checking product quality throughout all phases of manufacturing. It is the creation of work and product design procedures that are based on planning and supported by high-quality manuals and tools to avoid errors from arising in the first place.
The most important thing to remember is that clients ask for your quality plan because they want to know how you’ll manage the quality of their projects. As a result, while writing your plan, make it clear how you’ll manage all aspects of the project that affect quality, not simply the inspections and testing you’ll conduct. Controlling supplies, staff, subcontractors, and work practices, for example, is critical to achieving high-quality outputs. Finally, your quality strategy should give your clients confidence that your quality controls will help them receive the high-quality project they expect.
10+ Project Quality Control Plan Samples
1. Project Quality Control Plan Template
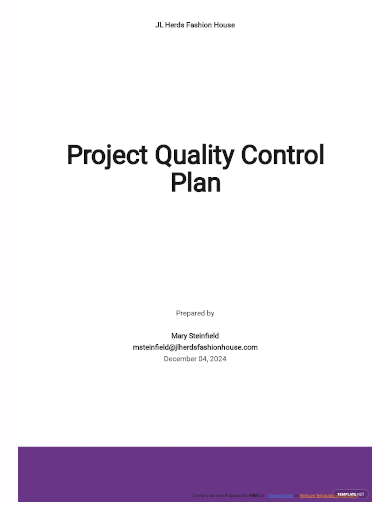
2. Project Management Quality Control Plan Template
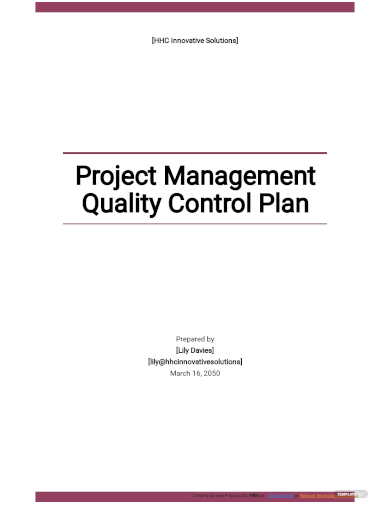
3. Consultant Project Quality Control Plan
4. Project Coordinator Quality Control Plan
5. Project Quality Control Plan
6. Project Quality Assurance Control Plan
7. Project Manager Quality Control Plan
8. Construction Project Quality Control Plan
9. Sample Project Quality Control Plan
10. Standard Project Quality Control Plan
11. Water Project Quality Control Plan
What is a Project Quality Control Plan
A project quality control plan, also known as a quality management plan, quality assurance plan, or project quality management plan, is a project-specific quality plan that outlines the activities, standards, tools, and processes required to ensure project quality. It’s commonly confused with the project execution plan (PEP), which lays out the general strategy for project management, explains who does what and how, and lays out the policies, processes, and priorities to be followed.
To a client, quality control might mean a variety of things. As a result, the first step is to figure out what your client wants. This can exist in the form of a specification or a remark in one of the contract documents. Other times, your customer will simply state that they require a quality control plan and leave it up to you to choose what they require. Nonetheless, it’s worthwhile to strike up a conversation to have a greater grasp of what they’re thinking or, at the very least, to ensure that they’re comfortable with your offer.
Essential Elements of a Project Quality Control Plan
- Project personnel – Every project should have a quality manager who is solely responsible for the project’s quality. Your client has to know who this individual is and what his or her obligations are in terms of quality. As a result, incorporate this information, as well as the person’s qualifications for the position, in your quality plan.
- Quality communications – Do you plan to hold a project kick-off meeting as well as regular production meetings to discuss quality issues? Will you be sending your client reports, test results, and/or inspection forms? Then, as part of your quality strategy, you should include a quality communications plan that outlines the expected touchpoints with your client.
- Quality assurance surveillance – With this in mind, your client will anticipate some type of quality control monitoring. Will you be checking on the quality of the project on a weekly or monthly basis? What will you be looking at? Include everything in your project quality plan so your client has a clear image of how you’ll keep the project on schedule.
- Subcontractors and suppliers – Outside groups play an important role in sourcing resources and completing construction projects. Tell your client who your primary suppliers and subcontractors will be for their project. What criteria do you employ to choose your subcontractors and suppliers? You most likely checked that they were competent in doing the service or offering quality materials in addition to the price.
- Project quality specifications – You will follow your customer’s instructions to the letter. In many circumstances, however, the client specifications do not specify whether building codes or industry standards apply to your project. Make a list of them so that you don’t get confused about which versions of which standards apply to your project.
- Inspections and tests – You should make a list of all the inspections and tests that you anticipate conducted during the project. Include the inspection forms and test reports you’ll need when the time arrives.
- Control of nonconformances – Everyone recognizes that things go wrong in construction from time to time. How you will manage these issues should be discussed in your quality plan. Make it clear how you’ll handle nonconformances to protect the project’s overall quality.
- Project completion inspections – So far, everything we’ve talked about has been about particular jobs and periods of labor. You should also talk about how you’ll conduct inspections and punch out near the end of the project to ensure that all of the contractual work is done correctly.
FAQs
What is another example of a quality plan?
A manufacturing company that machines metal parts are an example of a quality plan. Its quality plan includes relevant procedures such as descriptions of the manufacturing process and duties, applicable workmanship standards, acceptable measurement tolerances, material standards descriptions, and so on. All of them might be individual documents.
What is project quality?
The quality of a project includes not only the final deliverables but also the methods that will be employed to generate the product. It’s all about delivering a defect-free product that’s been developed as efficiently as possible. The quality management plan will cover both how to manufacture a defect-free product and how to use processes to their full potential.
The organization of individuals responsible for quality control, as well as the precise methods used to ensure the delivery of a quality product, will be identified in a quality control plan. A quality control plan will also include quality assurance procedures, accountability methods, and documentation requirements.
Related Posts
FREE 8+ Debt Management Plan Samples in PDF | DOC
FREE 10+ Sales Management Plan Samples in PDF | MS Word | Apple Pages | Google Docs
FREE 4+ 30-60-90-Day Marketing Plan Samples in MS Word | Google Docs | Apple Pages | PDF
FREE 10+ Higher Education Lesson Plan Samples in MS Word | Pages | Google Docs | PDF
FREE 9+ 30-Day Marketing Plan Samples in PDF | MS Word | Apple Pages | Google Docs
FREE 3+ Sales Team Action Plan Samples in PDF | MS Word | Apple Pages | Google Docs
Marketing Plan For Small Business Samples
FREE 7+ Fashion Business Plan Samples in PDF
FREE 10+ Sprint Planning Samples In MS Word | Google Docs | PDF
FREE 10+ Wedding Planning Samples in MS Word | Apple Pages | Powerpoint | PDF
FREE 9+ Monthly Study Planner Samples in PSD | Illustrator | InDesign | PDF
FREE 9+ Sample Curriculum Planning Templates in PDF | MS Word
FREE 10+ Teacher Development Plan Samples in MS Word | Google Docs | Apple Pages | PDF
FREE 10+ Basketball Practice Plan Samples in PDF
FREE 12+ School Business Plan Samples in PDF | MS Word | Apple Pages | Google Docs