Businesses that manufacture goods and other various products should always have a quality control team and procedure to ensure that the products they put out are of the best quality possible. To organize everything smoothly, outlining a quality control plan first before diving headfirst into the procedure can help streamline a business’s assurance procedure by specifically defining protocols and processes, employee duties, and potential responses. If you want your business to have an effective quality control plan, this article will guide you on how to create one. Keep reading the article below.
8+ Product Quality Control Plan Samples
1. Product Quality Control Plan Template
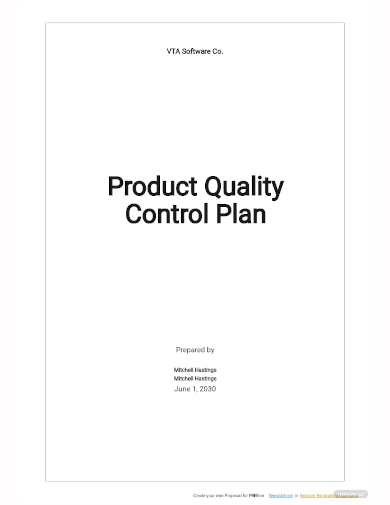
2. Product Quality Control Plan
3. Product Quality Assurance Control Plan
4. Sample Product Quality Control Plan
5. Product Supply Quality Control Plan
6. Advanced Product Quality Control Plan
7. Standard Product Quality Control Plan
8. Product Realization Quality Control Plan
9. Product Quality Process Control Plan
What is Quality Control?
Quality control is the final step of the stage of manufacturing products before it is being sent to distributors. This is where inspections and corrections procedures are done to ensure that all products being sent off to distributors meet the quality standards set by authoritative agencies. Quality control is essential in every business producing goods because sending sub-standard products to consumers may lead to undesirable events such as damaged reputation, decreased retention, and increased returns of defective products.
How to Create a Product Control Plan
1. Create an Organization Chart
Before you dive headfirst in outlining your quality control plan, you should first outline an organizational chart of your employees assigned to quality control and state their job descriptions, qualifications, and training they’ve undergone that are required to perform each quality assurance procedure. This is important to show documentation that all employees are qualified to be part of the quality control team.
2. Define the Duties of Each Employee Assigned in Quality Control
The next thing to do is to outline the duties of internal employees and external affiliations of the quality control team. Be specific in outlining each duty to ensure every party understands what processes they are responsible to do and they will be aware of who will be assigned to check the quality of their work too. Make sure this documentation is easily accessible to every employee.
3. Purchase Materials Needed For Quality Control
When purchasing materials, make sure that the specification of each material component must be correct and ensure that the suppliers providing the products must meet the desired quality standards of the business. Create a protocol for inspecting materials received and their key characteristics to check if they are correct and if they pass the quality standard test.
4. Verify Suppliers’ Qualifications
Aside from the materials being inspected for their quality, there should also be a protocol on how to screen the background of every supplier offering a bid to the business. The protocol must outline the process of how they will verify each supplier’s qualifications and the materials they provide through their reputation, brand, and the process on how they manufacture and supply other businesses.
5. Evaluate Feedback
Aside from relying on quality assurance to determine the quality of a certain good or product, it’s also essential to gain feedback from customers from the products or goods that were already released and been used by customers. Investigating online reviews, user complaints, and suggestions can help you determine the product’s strengths and weaknesses. Assign a customer service team that examines all the complaints and reviews of the customers and determines the common issues of the products and reports these findings to management. By doing this can help the business change the shortcomings of the product and improve it.
6. Create Corrective Action Plan
You should also establish a corrective action plan to solve quality issues, such as violations and non-compliance, and the process of reporting these issues and addressing them to mitigate these issues. You should also create a plan on how to prevent issues from reoccurring again that could disrupt your operations. Some examples of these are quality checks or installing automated software to check inventory.
FAQs
What are the different types of quality control tools?
Some examples of quality control tools are checklists, fishbone diagrams, control charts, stratification, Pareto chart, histogram, and scatter diagrams.
What is the difference between internal and external quality control?
Internal quality control is when a company establishes an in-house protocol to check their operation system, such as having routine checking of equipment, having a coworker go over another employee’s data analysis. etc. External quality control is when the products or data are sent to an outside business not affiliated with the company or by a third party to do the quality control testing.
Once you’re done creating your quality control plan, gather your employees and discuss the plan with them. Welcome any concerns, suggestions, and recommendations from them. Double-check to see that every process or procedure is outlined correctly and all inaccurate information is removed. To help you get started making the quality control plan, download our free sample templates above to use as your guide!
Related Posts
FREE 7+ Fashion Business Plan Samples in PDF
FREE 10+ Sprint Planning Samples In MS Word | Google Docs | PDF
FREE 10+ Wedding Planning Samples in MS Word | Apple Pages | Powerpoint | PDF
FREE 9+ Monthly Study Planner Samples in PSD | Illustrator | InDesign | PDF
FREE 9+ Sample Curriculum Planning Templates in PDF | MS Word
FREE 10+ Teacher Development Plan Samples in MS Word | Google Docs | Apple Pages | PDF
FREE 10+ Basketball Practice Plan Samples in PDF
FREE 12+ School Business Plan Samples in PDF | MS Word | Apple Pages | Google Docs
FREE 7+ Client Strategic Plan Samples in PDF | MS Word
FREE 11+ Trucking Business Plan Templates in PDF | MS Word | Google Docs | Pages
FREE 7+ Small Hotel Business Plan Samples PDF | MS Word | Apple Pages | Google Docs
FREE 14+ Bakery Business Plans in MS Word | PDF | Google Docs | Pages
FREE 4+ Yearly Lesson Plan Samples in PDF
FREE 50+ Strategic Planning Samples in Google Docs | Pages | PDF | MS Word
FREE 10+ Construction Project Plan Samples in MS Word | Google Docs | Apple Pages | PDF