If you’re looking for a reputable firm or organization, you might consider quality. When someone owns or runs a business, they are constantly striving for adequate performance. Is there a distinction in the quality of manufactured goods and services? Is the quality of the raw materials utilized in their manufacture acceptable? Anyone creating something for their investors, stakeholders, or clients ensures that it satisfies their requirements. It is critical to ensure the manufacturing and sale of high-quality goods and services. They take numerous critical steps to ensure that the product they produce is marketable. They must ensure that numerous factors are in place to ensure that these stages go well and that their product always maintains the highest possible quality. And effective control plans are tasked with the responsibility of determining these parameters.
To guarantee that the end product meets quality standards, rigorous preparation is critical. It saves both time and money by decreasing the risk of defective goods being made or assembled. Additionally, excellent action plans are particularly useful in this area. A quality management system not only communicates the high standard of quality that a business or organization aspires to, but it also details the activities and procedures that, when followed correctly, will ensure the greatest possible quality of the end output. You can gain a better knowledge of how a mortgage broker quality control plan works by reviewing the examples provided below, which will help you define what it is and how to implement it. Additionally, you can use them as a reference in developing your own control approach.
8+ Mortgage Broker Quality Control Plan Samples
1. Mortgage Broker Quality Control Plan Template
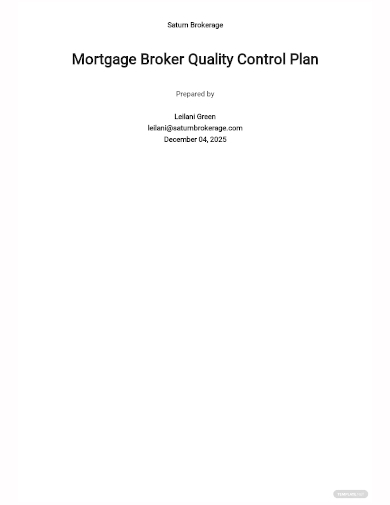
2. Mortgage Broker Quality Control Plan
3. Mortgage Broker Approval Quality Control Plan
4. Mortgage Broker Applicant Quality Control Plan
5. Wholesale Mortgage Broker Quality Control Plan
6. Mortgage Broker Policy Quality Control Plan
7. Mortgage Broker Company Quality Control Plan
8. Sample Mortgage Broker Quality Control Plan
9. Mortgage Broker Executive Quality Control Plan
What Is a Mortgage Broker Quality Control Plan?
The final step a business takes before releasing anything into the world. Producers perform a variety of various tasks at this stage of the process to ensure that the goods fulfill quality standards. These include quality assurance and change management.
This is a critical step in ensuring that the consumer receives their order. If you do not provide high-quality goods, you risk developing a negative image, losing clients, and receiving more returns.
Additionally, quality control examines how a product is manufactured, kept, and distributed to ensure its quality. When something is not good enough or is broken, the term “defective” is used. In this way, firms must ensure the safety of their products along the supply chain.
Internal and external quality control measures may be employed in combination depending on the type of business and the products sold by the company, and both may be necessary. Individuals who work for businesses with their own set of regulations might demonstrate internal control in the following ways: Repairing equipment, assessing staff performance, and everything in between may all be a part of the work. They ensure that quality assurance procedures are carried out correctly and on time.
On the other hand, products that are sold to other people require quality control by someone outside the organization. Individuals who work for other firms must inspect food after it is prepared and distributed to ensure that it is safe and has not spoiled before it can be sold in stores.
Qualified Control Plan: This is a written description of procedures and actions designed to ensure that the goods manufactured for a project meet the quality standards specified in the contract, other procedures and manuals, and other guidance. The term QCP refers to a Quality Control Plan.
How To Write a Mortgage Broker Quality Control Plan
1. Define an organizational chart
Management should begin by creating a chart outlining the roles, responsibilities, and training associated with each quality assurance technique. This is the first step they should take to ensure that everything is configured properly. These requirements must be documented to demonstrate that the individuals conducting inspections are properly qualified and informed about their jobs. This document should be retained in order for senior management to review it in the event of an issue or error. This manner, they can immediately rectify the situation. Because they can see what occurred, they may deduce what occurred.
2. Define responsibilities
Managers should then ensure that everyone understands their roles both within and outside the organization. Each partner should understand what they are responsible for and who will ensure their work is of high quality. Certain small enterprises permit their employees to inspect the quality of their work. While the majority of businesses do not permit this, some do. To ensure that each project has adequate time, different documentation must be created. This is because multitasking may result in additional errors. On the other hand, people who work for large firms appreciate it when multiple members of the same department review their coworkers’ work. These quality assurance criteria should be clear and unambiguous to minimize confusion and to ensure that each stage is completed thoroughly.
3. Purchase and receive materials
Prior to ordering supplies, managers should ensure that they have a firm grasp on the specifications. This manner, companies may be certain that the components they purchase satisfy the desired quality criteria. To save money, some businesses look for the lowest-priced vendors. This may eventually cause them to fall short of their quality assurance criteria. As a result, before you begin the ordering process, it is critical to determine the critical characteristics of the materials. The items have been delivered, and now that they have arrived, workers should inspect the shipment to ensure that all products fulfill the applicable criteria. It is the company’s responsibility to return things to the supplier if they do not fit their specifications.
4. Verify Suppliers’ Qualifications
You can readily inspect the quality of fundamental supplies. However, inspecting more intricate parts and equipment for quality might take a long time and be difficult. Firms should have a clear idea of what they want from vendors before soliciting bids. When organizations want to ensure that their internal procedures adhere to the standards, they might request an outside audit of a vendor to ensure compliance. Before concluding a transaction, conduct a background check on the supplier. Their brand and credentials should also be evaluated prior to hiring them.
5. Evaluate Quality Feedback
Before products are placed on the market, quality assurance personnel ensure that they are fit for sale. However, it is beneficial for you to provide comments on how a product functions and appears. Businesses can determine the quality of a product by examining internet reviews, customer complaints, and suggestions from other customers. This is their method. Having a customer service staff that reviews evaluations and compliance records to see whether problems were caused by rules violations is a smart idea if you own a firm. Individuals who work for the government are required to notify the government if they discover something is wrong.
6. Develop a process for corrective action
Finally, businesses must devise a strategy for resolving quality issues, such as violating the law or failing to follow the standards. When a non-compliant process is reported, the quality control person is responsible for investigating what occurred. This could be as a result of a mistake or because an employee failed to perform their duties. After determining the root source of the problem, a preventative solution must be implemented. This will ensure that the same issue does not happen again. Additional quality checks or automated technologies, such as inventory ordering systems, may be included in this package. If a product is recalled or has other issues, quality control plans assist organizations in ensuring that the proper procedures are taken to resolve the issue. This demonstrates to clients that a business cares about them and strives to create the greatest products possible.
FAQs
What are the three types of quality?
Professionals frequently classify quality faults into three categories: minor flaws, major flaws, and critical flaws, the most serious. Those with minor defects account for fewer than 1% of the total. According to the type of defect, it is assigned to a group with other problems of the same type.
What are the four types of quality control?
Process Control. Control Charts. Product Quality Control. Process Control.
What are action steps?
The action steps are the steps you take to accomplish the objectives outlined in your action plan. They are the actions you do to achieve them. Finally, what you write in your action plan is what constitutes the entire document.
Well-written action plans ensure that your business or organization’s goals, or even your own personal goals, are met or exceeded. It may bring your ideas to life. It can help you keep your project on track and eliminate any potential issues. It’s the same process for creating a good action plan. It helps you maintain a certain level of quality in your products and services while also encouraging continuous improvement.
Related Posts
FREE 9+ 30-Day Marketing Plan Samples in PDF | MS Word | Apple Pages | Google Docs
FREE 3+ Sales Team Action Plan Samples in PDF | MS Word | Apple Pages | Google Docs
Marketing Plan For Small Business Samples
FREE 7+ Fashion Business Plan Samples in PDF
FREE 10+ Sprint Planning Samples In MS Word | Google Docs | PDF
FREE 10+ Wedding Planning Samples in MS Word | Apple Pages | Powerpoint | PDF
FREE 9+ Monthly Study Planner Samples in PSD | Illustrator | InDesign | PDF
FREE 9+ Sample Curriculum Planning Templates in PDF | MS Word
FREE 10+ Teacher Development Plan Samples in MS Word | Google Docs | Apple Pages | PDF
FREE 10+ Basketball Practice Plan Samples in PDF
FREE 12+ School Business Plan Samples in PDF | MS Word | Apple Pages | Google Docs
FREE 7+ Client Strategic Plan Samples in PDF | MS Word
FREE 11+ Trucking Business Plan Templates in PDF | MS Word | Google Docs | Pages
FREE 7+ Small Hotel Business Plan Samples PDF | MS Word | Apple Pages | Google Docs
FREE 14+ Bakery Business Plans in MS Word | PDF | Google Docs | Pages