If you want to find a good business or company, you might want to look for quality. When someone owns or runs a company, they always want it to be good enough. Is there a difference in the quality of the products and services that are made? Is the quality of the resources that are used to make them? Anyone who is making something for their investors, stakeholders, or clients makes sure that it meets their needs. It’s important to make sure that high-quality products and services are made and sold. They do a lot of important things to make sure that what they make is good enough for the market. They need to make sure that a lot of things are in place for these stages to go smoothly and for the best possible quality of their product to be always achieved. And good control plans are in charge of setting these parameters, and they do it well.
In order to ensure that the finished product fulfills quality requirements, meticulous planning is essential. It saves both time and money by reducing the likelihood that goods will be defective after they have been manufactured or assembled. High-quality action plans are also extremely effective in this regard. A quality management system not only provides a clear image of the high level of quality that the company or organization is attempting to achieve, but it also lays out the actions and procedures that, if followed correctly, will ensure that the final product is of the highest possible quality. You may learn more about how a software quality control plan works by looking at the examples provided below, which will give you a better understanding of what it is and how to implement it. Also, you can use them as a guide to assist you in drafting your own control strategy.
3+ Construction Quality Control Management Plan Samples
1. Construction Quality Control Management Plan Template
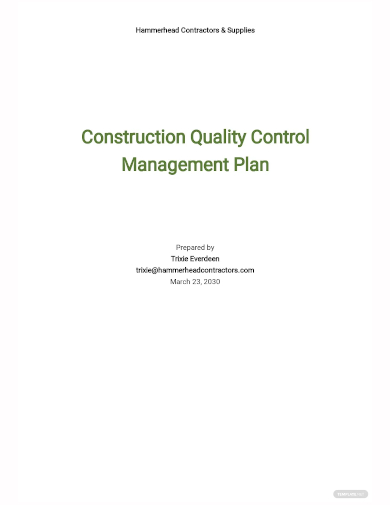
2. Construction Quality Assurance Management Plan
3. Construction Quality Control Contract Management Plan
4. Construction Management Quality Control Plan
What Is a Construction Quality Control Management plan?
Last thing a company does before they put something out into the world. To make sure that the goods meet quality standards, producers do a lot of different things at this point in the process. These include things like quality checks and making changes.
To make sure that the customer gets their order, this is an important step. If you don’t make high-quality goods, you could get a bad reputation, lose more customers, and get more returns.
Also, quality control looks at how a product is made, stored, and sent out to make sure it’s good. There are times when something isn’t good enough or broken, and people use the word “defective.” In this way, businesses need to make sure their products stay safe through all stages of the supply chain.
Internal and external quality control measures may be used depending on the type of business and the types of products that a company sells, so it may be necessary to use both. People who work for businesses that have their own rules can show internal control in this way: Fixing equipment, looking at how well employees are doing, and everything else in between could be part of the job, too. They make sure that quality assurance procedures are done the right way and at the right time.
Products that are sold to other people, on the other hand, need to be checked for quality by people outside of the company. People who work for other businesses must check the food after it is made and distributed to make sure it is healthy and hasn’t gone bad before it can be sold in stores.
Qualified Control Plan: This is a written list of procedures and actions that are meant to make sure the goods made for a project meet the quality standards that were set out in a contract and other procedures and manuals, as well as in other guidance. QCP stands for Quality Control Plan.
Elements of a Construction Quality Control Management plan
- Define an organizational Chart
Management should start by making a chart of jobs, qualifications, and training for each quality assurance method. This is the first thing they should do to make sure everything is set up correctly. These standards must be written down to show that the people who do inspections are well-trained and knowledgeable about their work. This document should be kept on file so that senior management can see it if there is a problem or an error. This way, they can fix it quickly. Because they can see what happened, this way, they can figure out what happened. - Define responsibilities
Managers should then make sure everyone knows what their roles are inside and outside the company. Each partner should know what they are supposed to do and who will make sure their work is good. The employees of some small businesses are allowed to check the quality of their work. Most businesses don’t let their employees do this, but some businesses do. In order to make sure that each project was given enough time, separate documents need to be made. This is because multitasking could lead to more mistakes. People who work for big companies, on the other hand, like it when different people in the same department look over the work of their co-workers. There should be no ambiguity in these quality assurance rules in order to avoid confusion and to make sure that each step is done as thoroughly as possible. - Purchase and receive materials
Before ordering materials, management should make sure they understand the specifications. This way, they can be sure that the parts they buy meet the quality standards they want. To save money, some businesses try to find vendors who charge the least. In the long run, this could make them fall short of their quality assurance standards. As a result, before you start the ordering process, it is important to figure out what the important qualities of the materials are. The materials have been delivered, and now that they are there, staff should check the shipment to make sure that all of the products meet the standards. It’s up to the company to return the items to the supplier if they don’t meet their standards. - Verify Suppliers’ Qualifications
You can easily check basic materials for quality. It can take a long time and be hard to check more complicated parts and equipment for quality, though. Firms should know what they want from vendors before they ask for bids. When businesses want to make sure their internal processes are in line with the rules, they can ask for an outside audit of a vendor to make sure they’re following the rules. Check out the supplier’s reputation before making a deal. Their brand and their credentials should also be looked at by them before they hire them, too. - Evaluate Quality Feedback
People in quality assurance make sure that the products are good enough to be sold before they go on sale. Then again, it’s very good for you to give feedback on how a product works and how well it looks. By looking at online reviews, customer complaints, and ideas from other customers, companies can figure out how good or bad a product is. This is how they do it. Having a customer care team that looks at evaluations and compliance records to see if problems were caused by not following rules is a good idea if you run a business. People who work for the government have to tell the government if they find out that something isn’t right. - Develop a process for corrective action
Finally, companies need to come up with a plan to fix problems with quality, like breaking the law or not following the rules. When a non-compliant process is reported, the person in charge of quality control must look into what happened. It could be because of a mistake or because an employee didn’t do their job. A preventative measure must be put in place after the root cause of the problem has been found. This will keep the same thing from happening again. In this package, there could be extra quality checks or automated tools, like inventory ordering systems, that could be used. If a product is recalled or there are other problems with it, quality control plans help businesses make sure that the correct steps are in place to fix the problem. This shows to customers that a company cares about them and wants to make the best products on the market.
FAQs
What are action steps?
Action steps are the things you do to reach the goals you set out in your action plan. They are the things you do in order to reach them. In the end, it’s what you write in your action plan that makes up the whole thing.
What are the four types of quality control?
Process Control. Control Charts. Product Quality Control. Process Control.
What are the three types of quality?
Professionals often break down quality flaws into three groups: minor flaws, major flaws, and critical flaws, which are the most important. Those that aren’t major flaws make up less than 1% of the whole. Based on what kind of defect it is, it is put into a group with other defects of the same kind.
Action plans that are well-written ensure that the objectives of your business or organization, or even your own personal objectives, are accomplished and even exceeded by the end of the day. You may see your thoughts come to life through it. It can assist you in keeping your project on track and avoiding any complications that may arise during the course of the procedure. It is essentially the same method for developing a successful action plan. It assists you in maintaining a specific degree of quality in your products and services while also ensuring that you are constantly striving to improve.
Related Posts
FREE 9+ 30-Day Marketing Plan Samples in PDF | MS Word | Apple Pages | Google Docs
FREE 3+ Sales Team Action Plan Samples in PDF | MS Word | Apple Pages | Google Docs
Marketing Plan For Small Business Samples
FREE 7+ Fashion Business Plan Samples in PDF
FREE 10+ Sprint Planning Samples In MS Word | Google Docs | PDF
FREE 10+ Wedding Planning Samples in MS Word | Apple Pages | Powerpoint | PDF
FREE 9+ Monthly Study Planner Samples in PSD | Illustrator | InDesign | PDF
FREE 9+ Sample Curriculum Planning Templates in PDF | MS Word
FREE 10+ Teacher Development Plan Samples in MS Word | Google Docs | Apple Pages | PDF
FREE 10+ Basketball Practice Plan Samples in PDF
FREE 12+ School Business Plan Samples in PDF | MS Word | Apple Pages | Google Docs
FREE 7+ Client Strategic Plan Samples in PDF | MS Word
FREE 11+ Trucking Business Plan Templates in PDF | MS Word | Google Docs | Pages
FREE 7+ Small Hotel Business Plan Samples PDF | MS Word | Apple Pages | Google Docs
FREE 14+ Bakery Business Plans in MS Word | PDF | Google Docs | Pages