Possibly the most important characteristic to look for in any business or company on this planet is quality. In any type of business, the owner or manager is constantly striving to achieve a certain level of excellence. There are a variety of factors that can influence this, ranging from product and service quality to the quality of the resources that are used to manufacture them. Everyone is concerned with making certain that everything they produce meets the expectations of their investors, stakeholders, and, most importantly, their customers and clients. When there is a demand for high-quality products and services, there is also a responsibility to ensure that those quality standards are met. They take a number of important steps to ensure that the product they produce is suitable for the market. There are numerous factors that must be in place for these stages to run smoothly and for the highest possible level of consistency in the quality of their product to be achieved. These parameters are set by good control plans, which are in turn set by good control plans.
In order to ensure that the final product meets quality standards, meticulous planning is essential. It saves both time and money by reducing the likelihood that items will be defective after they have been manufactured or assembled. High-quality action plans are also extremely effective in this regard. A quality management system not only provides a clear picture of the high level of quality that the company or firm is attempting to achieve, but it also lays out the actions and rules that, if followed correctly, will ensure that the final product is of the highest possible quality. You can learn more about how a project quality plan works by looking at the examples provided below, which will give you a better understanding of what it is and how to use it. Also, you can use them as a guide to assist you in drafting your own quality plan.
10+ Project Quality Plan Samples
1. Project Quality Plan
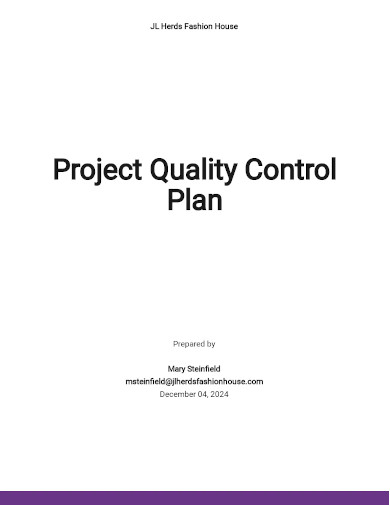
2. Project Quality Assurance Plan
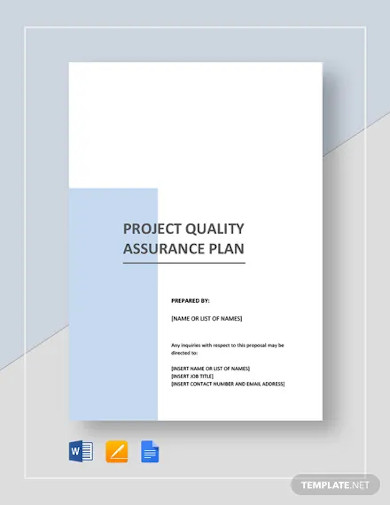
3. Project Management Quality Control Plan
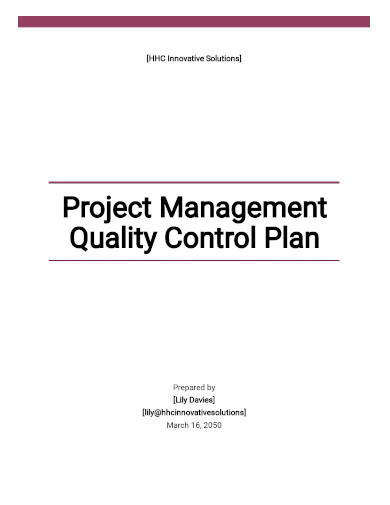
4. Sample Quality Assurance Project Plan
5. Simple Project Quality Plan
6. Project Quality Management Plan
7. Project Quality Assessment Plan
8. Basic Project Quality Plan
9. Formal Project Quality Plan
10. Project Quality Plan Example
11. Printable Project Quality Plan
What Is a Project Quality Plan?
It’s usually the last thing a company does before releasing a product into the public domain. During this stage of the manufacturing process, producers carry out a variety of tasks to ensure that the goods meet quality standards, including quality checks and corrections.
If the product is complete and ready to be shipped to the customer, this is an extremely important step in the process. If you fail to deliver high-quality goods, you may suffer from a tarnished reputation, lower customer retention, and increased returns.
Also included in the scope of quality control is the way a product is manufactured, stored, and distributed. When something isn’t good enough or is broken, the term “defective” is used to describe it. The result is that businesses must develop efficient systems that ensure the safety of their products at all stages of the manufacturing and distribution process.
If a company operates in a specific industry and sells a specific type of product, it may be necessary to implement internal and external quality control measures to ensure that the products are safe for customers to consume. Businesses that have their own set of rules can serve as an example of internal control mechanisms. This could include anything from repairing equipment to assessing how well employees are performing, as well as everything in between. Upper-level managers are responsible for ensuring that quality assurance procedures are carried out in the proper manner and at the appropriate time.
External quality control, on the other hand, is essential for products that are intended for sale to the general public. For example, after food has been produced and distributed, outside businesses must inspect the product to ensure that it is safe to consume and has not gone bad before it can be sold on the open marketplace.
In quality control, QCP is an abbreviation for Quality Control Plan. A Quality Control Plan is a written list of procedures and actions that are intended to ensure that the goods produced for a project meet or exceed the quality standards that have been set forth in the contract and in other policies and procedures, as well as in other guidance.
How To Write a Project Quality Plan
- Create an organization chart
The first step that management should take is to organize a chart of jobs, qualifications, and training for each quality assurance method. These standards must be documented to demonstrate that those conducting inspections are appropriately trained and competent. This document should be retained on file and made available to senior management in the event of a problem or error. This way, they will be able to see what occurred. - Define responsibilities
Following that, management must ensure that everyone understands their roles both inside and outside the organization. Each partner should understand their responsibilities and who will be responsible for ensuring their work is of high quality. While some small businesses allow employees to inspect their own work, the majority of businesses require these procedures to be performed by a separate group of people. This means that separate documents must be created to ensure that sufficient time was allocated to each project, as multitasking may result in increased human error. On the other hand, large companies prefer that different members of the same department check the work of their coworkers. These quality assurance specifications should be very specific in order to avoid confusion and to ensure that each step is completed thoroughly. - Purchase and receive materials
Prior to ordering materials, management should ensure that they have a firm grasp of the specifications. This way, they can be certain that the components they purchase meet the desired quality standards. To save money, some businesses look for the lowest-priced vendors. This may eventually cause them to fall short of their quality assurance standards. As a result, before you begin the ordering process, it is critical to determine the critical characteristics of the materials. After receiving the materials and verifying their presence, staff should inspect the shipment to ensure that all products meet the standards. It is the company’s responsibility to return items to the supplier if they do not meet their specifications. - Verify supplier’s qualifications
While it is simple to check the quality of basic materials, it can take a long time and be difficult to check the quality of more complicated parts and equipment. Before sending out a bid request, businesses should be crystal clear about the services they require from vendors. For instance, businesses could request a third-party audit of a vendor to ensure that their internal processes adhere to the rules. As a result, businesses should conduct due diligence on suppliers prior to entering into a contract. Additionally, they should verify their brand and credentials. - Evaluate quality feedback
Quality assurance is responsible for ensuring that products meet specifications before they are sold to customers. However, feedback is an excellent way to enhance a product’s performance and overall quality. Businesses can determine the quality of a product by examining online reviews, user complaints, and suggestions from other customers. If you own a business, you should have a customer care team that reviews evaluations and compliance records to determine whether non-compliance caused problems. If an employee discovers a process that is not in compliance with the law, they are required to report it. - Develop a process for corrective action
Finally, businesses must devise a strategy for resolving quality issues, such as violating the law or failing to follow the rules. When a non-compliant process is reported, the quality control person is responsible for investigating what occurred. This could be as a result of a mistake or because an employee failed to perform their duties. After determining the root cause of the problem, a preventative measure must be implemented. This will ensure that the same thing does not happen again. Additional quality checks or automated tools, such as inventory ordering systems, may be included in this package. Businesses can use quality control plans to ensure that all of their products meet expected standards and that corrective action is taken in the event of a product recall or other customer complaint. This demonstrates to customers that a business cares about them and strives to create the best products possible.
FAQs
What are the three types of quality?
Many professionals classify quality defects into three categories: minor flaws, significant flaws, and critical flaws. Minor flaws are those that account for less than 1% of the total. Defects are classified according to their nature and severity.
What are the four types of quality control?
Process Control. Control Charts. Product Quality Control. Process Control.
What are the action steps?
Action steps are specific actions taken to accomplish the goals outlined in your action plan. In essence, the content of your action plan is what it is about.
By the end of the day, well-written action plans ensure that the goals of your business or corporation, or even your own, will have been met and even exceeded. It breathes life into your concepts. It can assist you in keeping your project on track and avoiding potential issues that may arise during the process. It’s essentially the same process as creating an effective action plan. It enables you to maintain a certain level of quality in your products and services while also allowing for continuous improvement.
Related Posts
FREE 9+ 30-Day Marketing Plan Samples in PDF | MS Word | Apple Pages | Google Docs
FREE 3+ Sales Team Action Plan Samples in PDF | MS Word | Apple Pages | Google Docs
Marketing Plan For Small Business Samples
FREE 7+ Fashion Business Plan Samples in PDF
FREE 10+ Sprint Planning Samples In MS Word | Google Docs | PDF
FREE 10+ Wedding Planning Samples in MS Word | Apple Pages | Powerpoint | PDF
FREE 9+ Monthly Study Planner Samples in PSD | Illustrator | InDesign | PDF
FREE 9+ Sample Curriculum Planning Templates in PDF | MS Word
FREE 10+ Teacher Development Plan Samples in MS Word | Google Docs | Apple Pages | PDF
FREE 10+ Basketball Practice Plan Samples in PDF
FREE 12+ School Business Plan Samples in PDF | MS Word | Apple Pages | Google Docs
FREE 7+ Client Strategic Plan Samples in PDF | MS Word
FREE 11+ Trucking Business Plan Templates in PDF | MS Word | Google Docs | Pages
FREE 7+ Small Hotel Business Plan Samples PDF | MS Word | Apple Pages | Google Docs
FREE 14+ Bakery Business Plans in MS Word | PDF | Google Docs | Pages