Possibly the most important distinguishing characteristic of any business or organization on the planet is its commitment to quality. In order to be successful, any type of business or business owner strives to maintain a high level of quality, which they strive to maintain on a consistent basis. Product quality, services quality, and resource quality are just a few examples of what could be considered. Ensure that everything you produce meets the expectations of your investors, stakeholders, and, most importantly of all, your customers. Furthermore, the requirement for high-quality products and services is accompanied by the obligation to ensure that those quality standards are met. To ensure that whatever they produce is suitable for the market, a number of significant efforts are put forth by the company. A number of factors must be established in order for these stages to be successfully completed and the highest possible quality of their product to be consistently obtained. In order to establish these parameters, effective control plans must be implemented.
There can never be enough emphasis placed on the importance of planning when it comes to ensuring that the final product meets quality standards. It helps to save time and resources by reducing the likelihood of defective items being produced after they have been designed and developed. Action plans of high quality are particularly effective in this regard. Non-only does it provide a clear picture of the high level of quality that the company or organization is attempting to achieve, but it also specifies actions and parameters that, if followed correctly, will ensure that the end result is of the highest possible quality. See the samples below to learn more about what goes into a quality control plan. You can use them to familiarize yourself with the document and even to create your own quality roadmap if you want to be more creative.
7+ Quality Mind Map Samples
1. Quality Service Mind Map
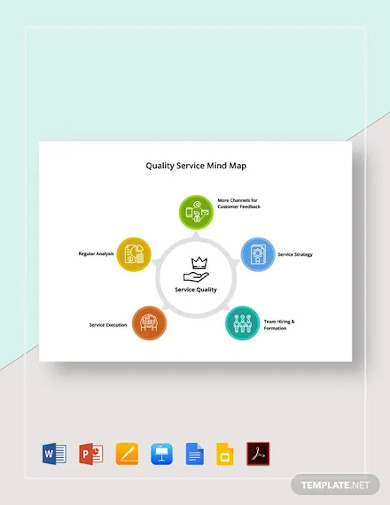
2. Quality Management Mind Map
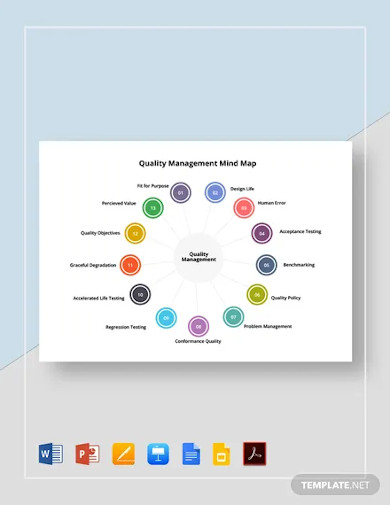
3. Quality Improvement Mind Map
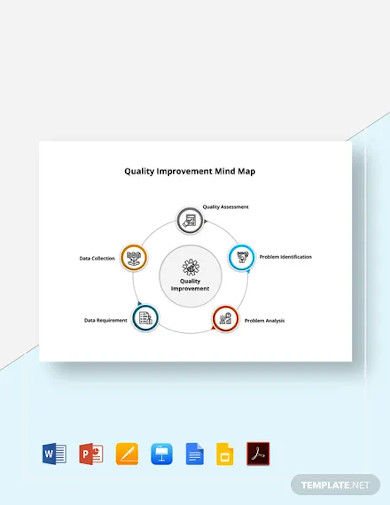
4. Data Quality Mind Map
5. Quality Memory Mind Map
6. Sample Quality Mind Map
7. Quality Service Transition Mind Map
8. Basic Quality Mind Map
What Is a Quality Mind Map?
When it comes to releasing a product into the marketplace, product quality control is frequently the last step to complete. Producers carry out a variety of operations, such as quality checks and corrections, during this stage of the manufacturing process to ensure that the goods produced meet quality standards.
When it comes to shipping, this stage is critical because it determines whether the product is ready to be delivered to the customer. Inability to deliver high-quality items can result in a tarnished reputation, decreased customer retention, and an increase in return requests.
Quality control also includes inspecting the processes used in the manufacture, storage, and distribution of a product. A “defective” product is one that is not up to standard or has been damaged in some way. Consequently, businesses must devise effective systems to ensure the integrity of their products at all stages of the supply chain throughout the entire process.
A company’s quality control measures may be required both internally and externally depending on the industry and the types of products distributed by the company. Firms that use internal protocols to communicate with one another are a common example of internal controls. This could include anything from equipment maintenance to employee performance evaluations, as well as everything else in between. Upper-level management is in charge of ensuring that quality assurance procedures are carried out in the proper manner and at the appropriate times.
The use of external quality control is required for products that are sold to third parties, on the other hand. When food is manufactured and distributed, for example, it must be checked by outside businesses to determine its nutritional value and expiration date before it can be sold to customers in the market.
It is an abbreviation for Quality Control Plan, and it is a written collection of procedures and actions designed to deliver goods that meet the quality objectives for a project as specified in contract contracts, other procedures and manuals, and other guidance. QCP stands for Quality Control Plan in English.
How to Write a Quality Mind Map
- Create an organization chart
In order to properly implement each quality assurance method, management must first develop an organizational chart that includes job descriptions, business qualifications, and the training required to properly implement each method. To demonstrate that inspectors have received proper training and are competent, these standards must be documented. It is recommended that this document be kept on file and presented to senior management in the event of a problem or error. - Define responsibilities
Following that, management must define the roles and responsibilities of all internal employees as well as those of outside affiliates. Each partner should be aware of the processes for which they are responsible, as well as who will be in charge of quality checking their work after it has been completed. Most businesses, with the exception of a few small businesses, require that quality control and verification procedures be carried out by a separate group of individuals. The creation of separate documentation is required to ensure that each task was given adequate time, as multitasking may result in an increase in the number of instances of human error. Large corporations, on the other hand, prefer that different members of the same department review the work of their coworkers in a centralized setting. These quality assurance specifications should be clearly defined in order to avoid confusion and to ensure that each step is carried out exactly as described in the specifications. - Purchase and receive materials
Management should thoroughly understand the specifications before ordering materials to ensure that the components ordered meet the desired quality standards. While seeking the lowest rates from vendors may save businesses money in the short term, it may cause them to fall short of quality assurance criteria in the long run. As a result, before beginning the ordering process, it is critical to identify the important qualities of the materials. Once the materials have been delivered, staff should inspect the shipment to ensure that all of the products meet the required standards. If the delivery falls short of expectations, the company must return the items to the supplier. - Verify Supplier’s Qualifications
While basic material inspection is relatively simple, performing quality assurance on more complex components and equipment can be time-consuming and difficult. As a result, before submitting a bid request, companies should clearly define their requirements and vendor expectations. Businesses, for example, could request that a vendor be audited by a third party to ensure that their internal processes are in accordance with applicable regulations. Then, before signing a contract, businesses should assess potential suppliers’ reputation, brand, and qualifications. - Evaluate quality feedback
The goal of quality assurance is to ensure that products meet specifications before they are distributed to customers. Feedback, on the other hand, is an excellent tool for improving product performance and overall quality. Companies can determine the advantages and disadvantages of a product by reviewing online reviews, user complaints, and suggestions from other customers. Organizations should form a customer service team that compares evaluations with compliance records to determine whether issues were caused by noncompliance. If an employee discovers that a procedure is not in accordance with the law, they must report the problem. - Develop a process for corrective action
Finally, companies must create a corrective action plan to address quality issues like infractions and regulatory noncompliance. When a non-compliant process is reported, it is the responsibility of the quality control employee to investigate the circumstances surrounding the occurrence. It could be the result of a malfunction or the negligence of an employee. Once the underlying cause has been identified, the company must take preventative measures to ensure that the event does not reoccur. Additional quality checks or automated tools, such as inventory ordering systems, could be included in this package. Businesses can use quality control plans to ensure that all products meet expected standards and that corrective actions are in place in the event of a product recall or other consumer complaints. This demonstrates to customers that a company values their input and is dedicated to providing the best products on the market.
FAQs
What are action steps?
Action steps are specific actions taken to achieve the objectives outlined in your action plan. In essence, it is all about the content of your action plan.
What are the three types of quality?
Quality flaws are frequently classified as minor, major, or critical by professionals. Minor flaws are defined as those that account for less than 1% of the total. The nature and severity of a defect are used to determine which category it should be assigned to.
What are the four types of quality control?
Process Control. Control Charts. Product Quality Control. Process Control.
A well-written action plan ensures that your company’s or corporation’s goals, as well as your own personal goals, are met and exceeded. To put it another way, it turns your dream into a reality. It can assist you in staying on track with your project and avoiding any potential roadblocks that may arise along the way. The method for creating a high-quality action plan is essentially the same. It allows you to maintain a certain level of quality in your products and services while also allowing for continuous improvement.
Related Posts
Argumentative Writing Samples & Templates
Contract Cancellation Letter Samples & Templates
Sample Material Lists
Sample Excuse Letter for School
Feature Writing Samples
FREE 10+ Security Guard Contract Samples in PDF | MS Word
FREE 10+ Option to Purchase Agreement Samples in MS Word | Apple Pages | PDF
FREE 26+ Curriculum Form Samples in MS Word | PDF
FREE 20+ Cleaning Service Proposal Samples in PDF | MS Word
FREE 29+ Sample Loan Application Form Templates in MS Word | PDF
FREE 10+ Event Venue Contract Samples in PDF | MS Word | Pages | Google Docs
FREE 10+ SBAR Samples in PDF | DOC
FREE 12+ Music Band Contract Templates in PDF | MS Word
FREE 10+ HVAC Maintenance Contract Samples in PDF | MS Word
FREE 10+ Social Media Marketing Contract Samples in MS Word | PDF